How We Improved Our Betonred In one Week(Month, Day)
페이지 정보
작성자 Lilliana 작성일 25-05-27 19:43 조회 40 댓글 0본문
Design Flexibility: Betonred can be molded into various shapes and forms, allowing for creative design possibilities. It can be combined with other materials, such as glass, steel, and wood, to create unique architectural features.
However, acid washing should be performed with caution and under proper supervision, as acids can damage the concrete surface. Thorough rinsing is essential after acid washing.
Poultices: Applying a poultice containing a chelating agent, such as EDTA, can help to draw out iron oxides from the concrete pores.
Re-sealing: After cleaning the surface, apply a high-quality concrete sealer to protect against future staining. Surface Cleaning: Mild cases of betonred (git.youbafu.cn) can often be removed by scrubbing the surface with a mild detergent solution or a specialized concrete cleaner.
Acid Washing: Diluted solutions of hydrochloric acid (muriatic acid) or phosphoric acid can be used to dissolve iron oxides.
These discolorations are primarily caused by the formation and deposition of hydrated iron oxides, also known as rust, and other iron-containing compounds. While often considered an aesthetic defect, understanding the underlying causes of betonred is crucial for preventing its occurrence and ensuring the longevity and durability of concrete structures. Betonred is not a single, well-defined chemical compound, but rather a descriptive term used in the concrete industry to refer to a family of reddish or pinkish discolorations that can appear on the surface of concrete.
The general reactions involved are: When iron is exposed to moisture and oxygen, it undergoes oxidation, forming iron oxides and hydroxides. This process is accelerated in the presence of chlorides or other aggressive chemicals that can break down the passive layer protecting the iron.
Material Selection and Proportioning: The selection of high-quality raw materials and their precise proportioning are crucial. This often involves laboratory testing to optimize the mix design for specific application requirements.
Cement: Portland cement, the primary binding agent in concrete, often contains small amounts of iron oxides as impurities.
Aggregates: Sands and gravels, the bulk of concrete mixtures, can also contain iron-bearing minerals like pyrite (FeS2), hematite (Fe2O3), and goethite (FeO(OH)).
Water: Potable water usually has minimal iron content, but groundwater sources, especially those passing through iron-rich soils, can contain dissolved iron.
Reinforcement Steel: Although protected by a passive layer of iron oxide in the alkaline environment of concrete, steel reinforcement can corrode under certain conditions, releasing iron into the concrete matrix.
Admixtures: Some concrete admixtures, particularly those containing iron-based pigments for coloration, can contribute to the overall iron content of the concrete.
Consider using supplementary cementitious materials (SCMs) like fly ash or slag to improve durability and reduce permeability.
Adequate Curing: Cure the concrete thoroughly for the recommended duration, using methods such as water curing, membrane curing, or steam curing.
Minimize Chloride Exposure: Use chloride-free admixtures and aggregates. Proper Concrete Mix Design: Use a low w/c ratio, appropriate cement content, and well-graded aggregates. Protect concrete surfaces from de-icing salts and marine spray. Consider using corrosion inhibitors to protect steel reinforcement in chloride-rich environments.
Ensure Proper Drainage: Design and construct concrete structures to ensure proper drainage and prevent water ponding.
Protective Coatings: Apply protective coatings, such as sealers or hydrophobic treatments, to the concrete surface to reduce water absorption and protect against aggressive environments.
Stainless Steel Reinforcement: In highly corrosive environments, consider using stainless steel reinforcement, which is highly resistant to corrosion.
Cost: Betonred is typically more expensive than traditional grey concrete due to the added cost of the pigments. However, the aesthetic benefits and potential long-term value often outweigh the higher initial cost.
Polished concrete surfaces with a red hue can add a modern and sophisticated touch to interior spaces. Interior Design: Betonred can also be incorporated into interior design elements such as countertops, flooring, and accent walls.
Therefore, it's crucial to understand the specific composition of the Betonred product being considered for a project. The term "Betonred," while sometimes used as a general descriptor, often refers to specific proprietary mixes or products offered by different manufacturers. These mixes might incorporate specialized admixtures or aggregates to enhance color vibrancy, durability, or workability.
Hematite (Fe2O3) is another common iron oxide that exhibits a reddish hue. Lepidocrocite (γ-FeO(OH)) is often associated with the early stages of corrosion and can appear as an orange or reddish-brown stain. The specific type of iron oxide formed depends on the pH, temperature, and the presence of other ions in the environment. Goethite (α-FeO(OH)) is a more stable form of hydrated iron oxide and can contribute to a more persistent discoloration.
However, acid washing should be performed with caution and under proper supervision, as acids can damage the concrete surface. Thorough rinsing is essential after acid washing.
Poultices: Applying a poultice containing a chelating agent, such as EDTA, can help to draw out iron oxides from the concrete pores.
Re-sealing: After cleaning the surface, apply a high-quality concrete sealer to protect against future staining. Surface Cleaning: Mild cases of betonred (git.youbafu.cn) can often be removed by scrubbing the surface with a mild detergent solution or a specialized concrete cleaner.
Acid Washing: Diluted solutions of hydrochloric acid (muriatic acid) or phosphoric acid can be used to dissolve iron oxides.
These discolorations are primarily caused by the formation and deposition of hydrated iron oxides, also known as rust, and other iron-containing compounds. While often considered an aesthetic defect, understanding the underlying causes of betonred is crucial for preventing its occurrence and ensuring the longevity and durability of concrete structures. Betonred is not a single, well-defined chemical compound, but rather a descriptive term used in the concrete industry to refer to a family of reddish or pinkish discolorations that can appear on the surface of concrete.
The general reactions involved are: When iron is exposed to moisture and oxygen, it undergoes oxidation, forming iron oxides and hydroxides. This process is accelerated in the presence of chlorides or other aggressive chemicals that can break down the passive layer protecting the iron.

Cement: Portland cement, the primary binding agent in concrete, often contains small amounts of iron oxides as impurities.
Aggregates: Sands and gravels, the bulk of concrete mixtures, can also contain iron-bearing minerals like pyrite (FeS2), hematite (Fe2O3), and goethite (FeO(OH)).
Water: Potable water usually has minimal iron content, but groundwater sources, especially those passing through iron-rich soils, can contain dissolved iron.
Reinforcement Steel: Although protected by a passive layer of iron oxide in the alkaline environment of concrete, steel reinforcement can corrode under certain conditions, releasing iron into the concrete matrix.
Admixtures: Some concrete admixtures, particularly those containing iron-based pigments for coloration, can contribute to the overall iron content of the concrete.
Consider using supplementary cementitious materials (SCMs) like fly ash or slag to improve durability and reduce permeability.
Adequate Curing: Cure the concrete thoroughly for the recommended duration, using methods such as water curing, membrane curing, or steam curing.
Minimize Chloride Exposure: Use chloride-free admixtures and aggregates. Proper Concrete Mix Design: Use a low w/c ratio, appropriate cement content, and well-graded aggregates. Protect concrete surfaces from de-icing salts and marine spray. Consider using corrosion inhibitors to protect steel reinforcement in chloride-rich environments.
Ensure Proper Drainage: Design and construct concrete structures to ensure proper drainage and prevent water ponding.
Protective Coatings: Apply protective coatings, such as sealers or hydrophobic treatments, to the concrete surface to reduce water absorption and protect against aggressive environments.
Stainless Steel Reinforcement: In highly corrosive environments, consider using stainless steel reinforcement, which is highly resistant to corrosion.
Cost: Betonred is typically more expensive than traditional grey concrete due to the added cost of the pigments. However, the aesthetic benefits and potential long-term value often outweigh the higher initial cost.
Polished concrete surfaces with a red hue can add a modern and sophisticated touch to interior spaces. Interior Design: Betonred can also be incorporated into interior design elements such as countertops, flooring, and accent walls.
Therefore, it's crucial to understand the specific composition of the Betonred product being considered for a project. The term "Betonred," while sometimes used as a general descriptor, often refers to specific proprietary mixes or products offered by different manufacturers. These mixes might incorporate specialized admixtures or aggregates to enhance color vibrancy, durability, or workability.
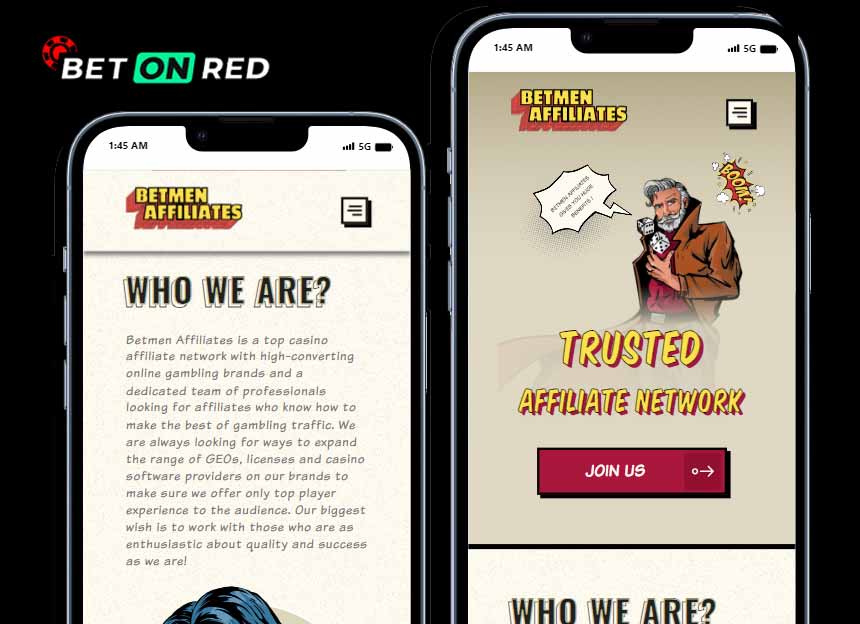
- 이전글 A Simple Trick For Voice Over Revealed8 Days To A greater Voice Over
- 다음글 There's By no means Just One Means To Weight loss plan
댓글목록 0
등록된 댓글이 없습니다.